In Chapter 2, we explained that we started this project with the help of 2 of our best customers who helped us to have 2 Buell XBRR. Andreas Kuehnle helped us to buy the bike number one. The plan was to use its engine for the race bike, while Peter Buedts lent us his XBRR to use the engine as a spare one.
We disassembled the race engine and we changed several parts in order to let it in perfect conditions. The next photo shows the engine ready to be assembled again.

And here we have the engine once we rebuilt it.
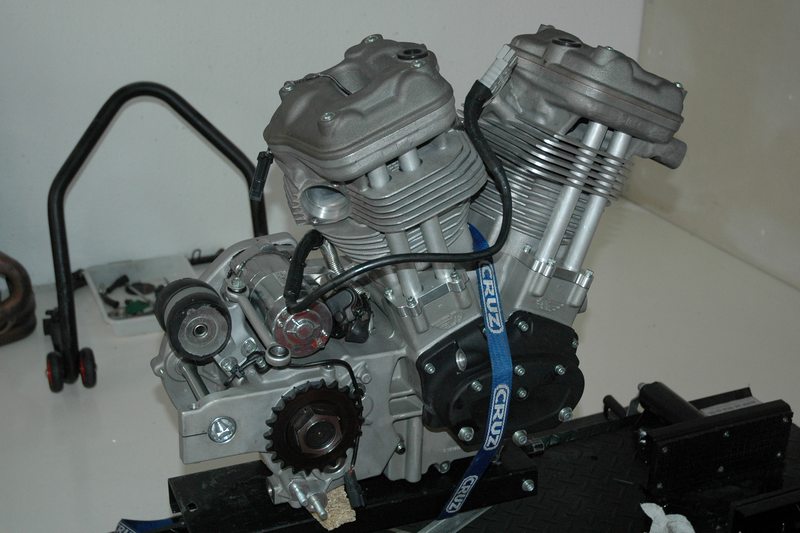
At that time we had the opportunity to sell the XBRR bike to one of our customers, and we did it. The next photo shows the XBRR after we rebuilt it.
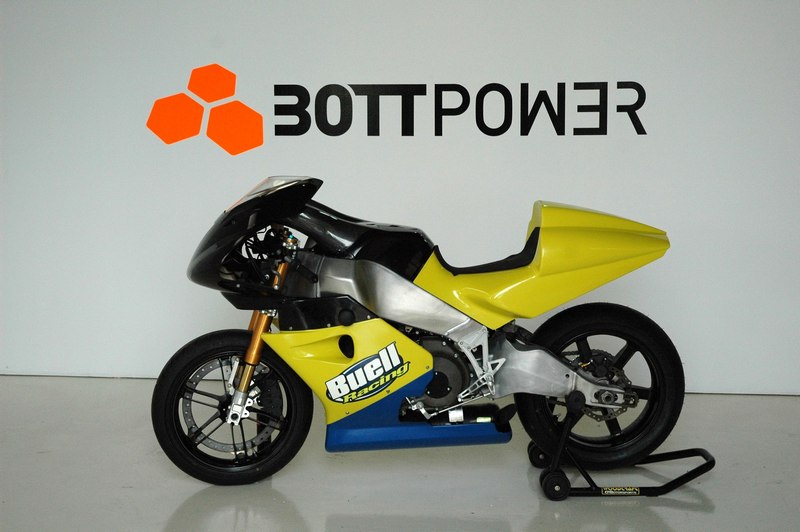
We sold the bike because we had located some brand new XBRR engines, so we didn’t need the complete XBRR anymore. We bought 3 engines, which are already in our workshop.

Selling the bike and buying the engines meant an important delay in our project, but at the same time, it allowed us to build our race bike using a brand new engine.
Now let’s talk about other parts that we were waiting for. We already received the new engine intakes, which have been milled in magnesium by Zanon, in Germany. This company made a great job with the intakes, they look perfect. The parts have a surface treatment to avoid magnesium corrosion.
This is the intake in the milling machine:
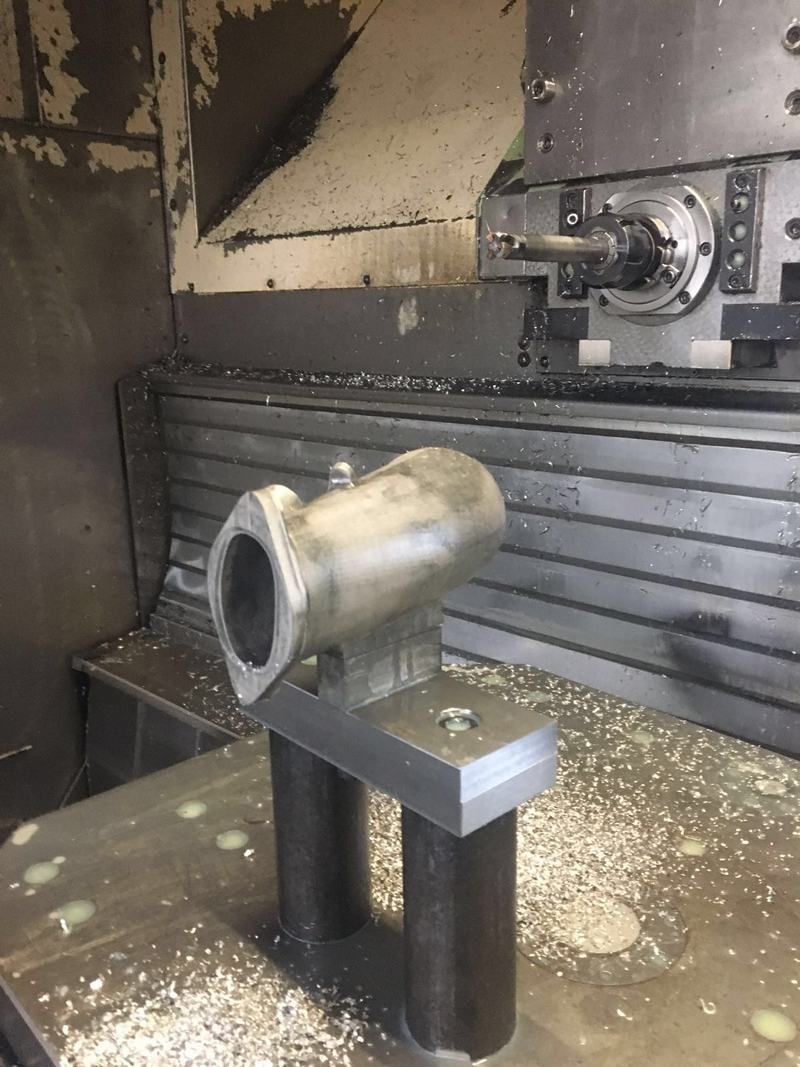
Here we have the finished parts:
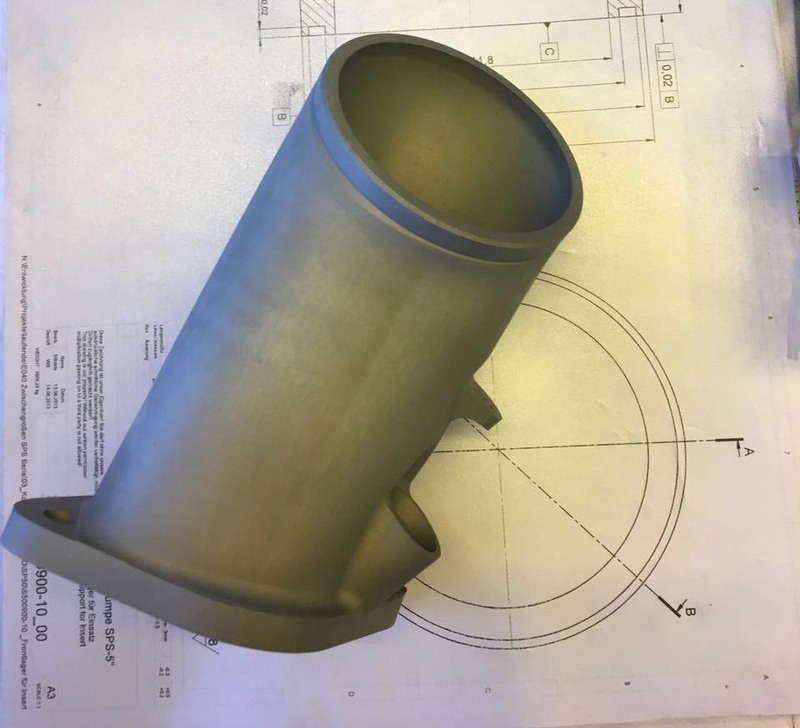
The next photo shows the Buell original magnesium intake (casted) and the new milled one.

We also received the titanium wheel axles.
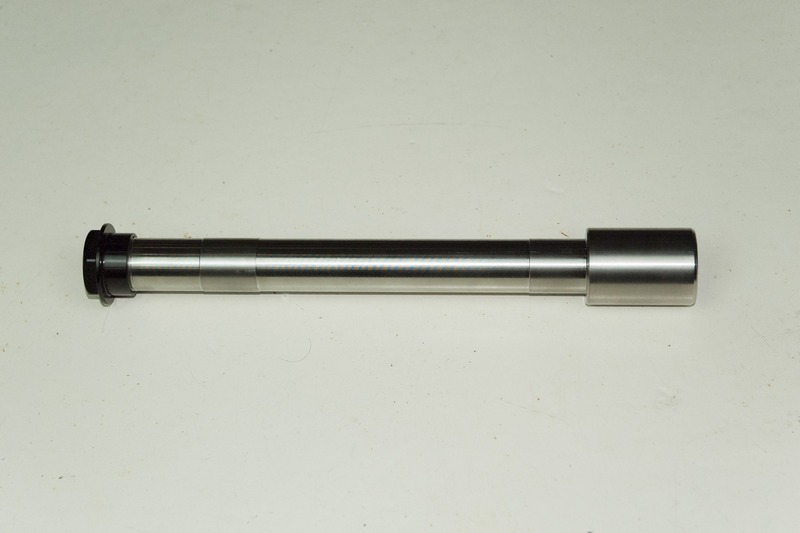
We also used titanium for the triple clamp axle. The photo shows the complete triple clamp, which has the same design of the Bottpower triple clamps that we use in our BOTT XR1 and XC1 bikes.
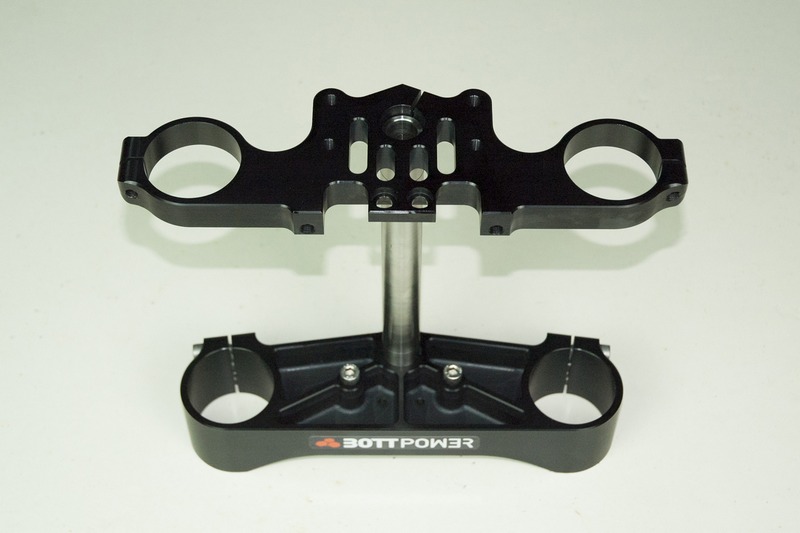
More details, next photo shows one of the Rotobox Boost carbon fiber rims that we are mounting on our race bike. The valve has a sensor that gives us information about the temperature and pressure of the air inside the tyre. We will talk about our data acquisition system in the next chapters.
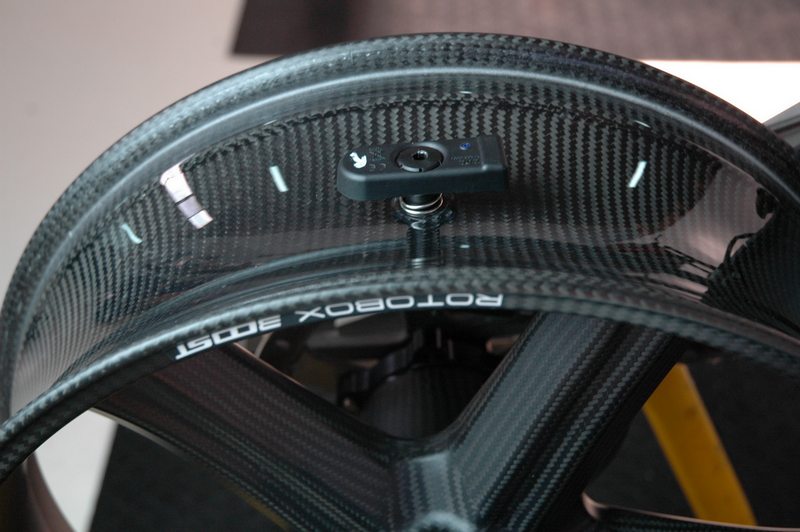
Here we have an image of the bike in our workshop. We took this photo before receiving the 3 XBRR engines.
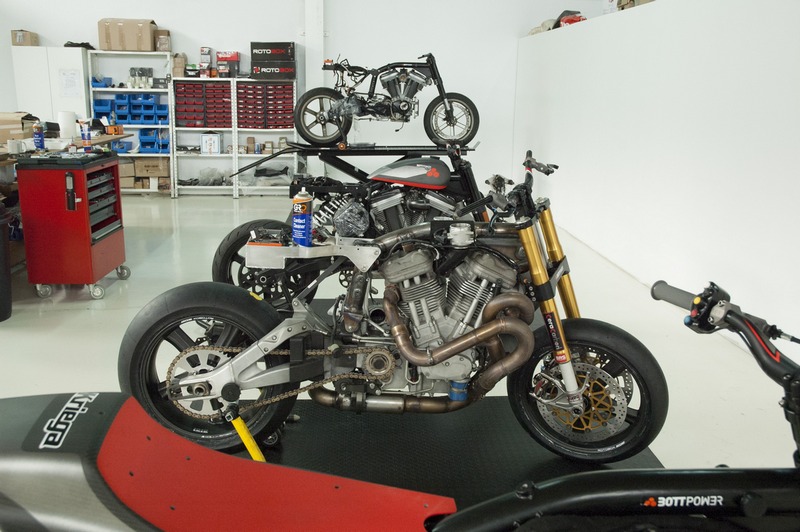
We already have all the components that we need to assembly the bike. The only part that is not fully finished yet is the airbox. We keep working on it and we hope to finish it next week. If everything is OK, we should “finish” the bike in a couple of weeks and then start doing the first tests.
As always, we remember you that it is still possible to buy some of the products that Kriega, our main sponsor, has created to help us to finance this project. Here you have an example, the BOTTPOWER URBAN EDC MESSENGER BAG:
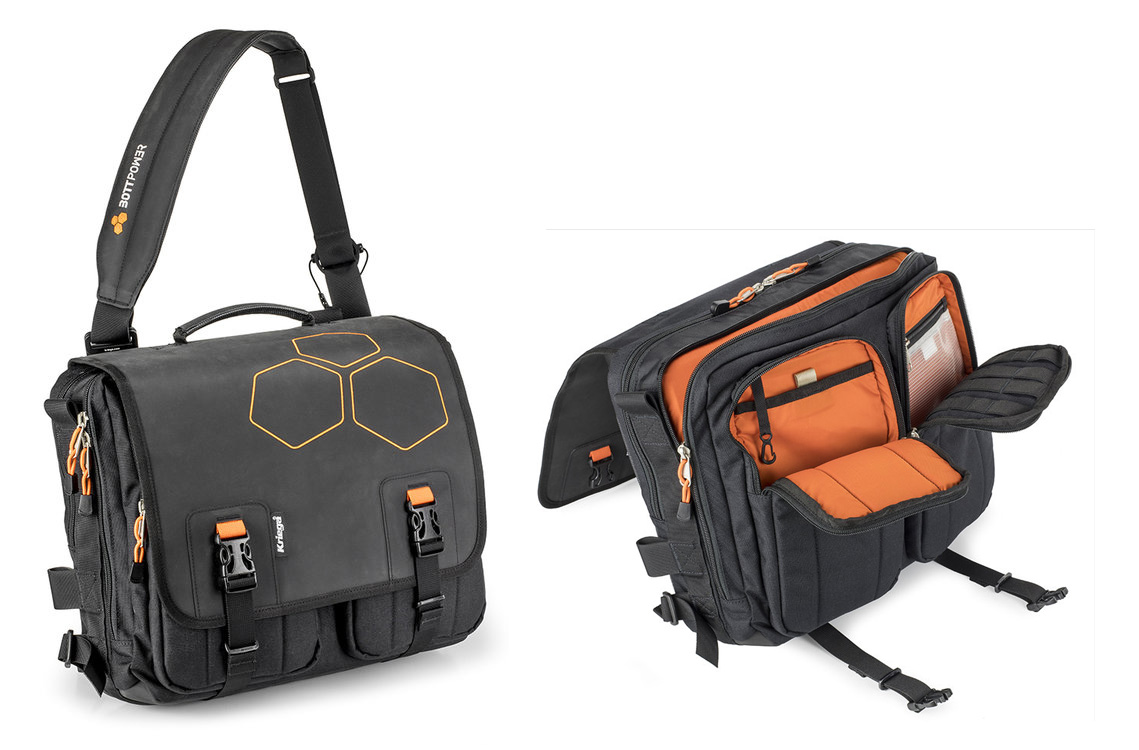
Thank you very much to everyone who already bought one of these cool Kriega/Bottpower products!
We also want to thank our sponsors: Kriega, Rotobox, CeraCarbon, Technical Composites, Continental Moto España, Global Racing Oil, Totimport, Derestricted, Husmee Studio Graphique, Sideburn Magazine, Motorbike Magazine, Newbold’s Motorbike Shop, Intelligent Design Solutions (IDS), Team BRS / BRS Suspension Works, and the last one to join us is Work & Wear, which will provide technical clothing (waterproof, thermal, breathable) for the Kriega-Bottpower Team. The race is at 4000 meters, so it is important to be properly equipped.
Without the support of these sponsors this project wouldn’t be possible!
Looking good! Can’t wait to see more. Are you familiar with Markforged 3D printing. They make printers that print parts out of metal, carbon fiber, and onyx (which is a plastic and chopped carbon fiber.). You can use them for structural parts that are prototype. (single part) I have seen them do several motorcycle parts. If you go to 3d Hubs they are a list of local 3d printing shops in your area and they might have a Markforged printer. You send them the cad files and they can print it off for you so you don’t have to buy a printer for a couple of parts. https://www.3dhubs.com http://www.markforged.com
Hi Charlie, thank you for your comment, it is very interesting.
We have a 3D printer that we use everyday (and many nights). All our bikes have 3D printed parts, that means that we do not use 3D printed parts only for prototypes, we use them also for some “production” parts.
For example the Moto2 bike that we built in 2010 had many functional 3D printed parts. Here you have an example of the airbox intake, which also supported the display and the bodywork:
https://www.flickr.com/photos/bottpower/5048127576/in/album-72157613166396341/
https://www.flickr.com/photos/bottpower/4751097363/in/album-72157613166396341/
We are already working on using 3D printed metallic parts that will form part of the frames we design and build.
I have been using 3D printing for more than 20 years, it is a technology that I love. It is clear that now is something that is spreading very fast and it is changing the way we design and fabricate everything.
In following chapters we will show the 3D printed parts that we will use on the XR1R for Pikes Peak.
It’s great to see more progress. I am curious about the fuel capacity, will the side tanks have enough or are you making larger ones.
Hi Bob, thank you for your clever comment. 🙂
We are making a little bit bigger side tanks. We will talk about it in next chapter.